5 things manufacturers can do to help us – by recyclers
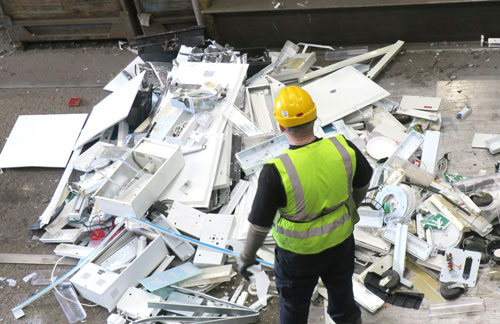
A leading recycler of luminaires has spelled out how manufacturers can make their products easier to reprocess.
Justin Greenaway, commercial manager of Kent-based SWEEEP Kuusakoski, one of the UK’s largest dedicated WEEE processing facilities, says there are simple measures light makers can do which would make a big impact.
• End the use of GRP
Greenaway says that his biggest headache with light fittings is glass reinforced plastic, or GRP. The composite material, commonly called fibreglass, is still widely used to make the housings of industrial and weatherproof luminaires with high IP ratings. But Greenaway says it’s complex and expensive to separate and recycle.
• Identify light sources
Another problem is light sources. While the Kent facility usually receives lights with the lamps already removed and sent to a specialist lamp recycling facility, Greenaway says it’s often difficult for his operatives to identify light sources in luminaires easily. He would like clear labels stating ‘LED’ or, better still, ‘mercury free’.
• Identify batteries
Batteries, too, are a challenge for recyclers. He also wants their location, especially small ones, to be identified clearly.
• Make batteries easy to remove
Removing batteries is a time-consuming headache for recyclers, but important as they can be a fire hazard if they make it into the shredder. So make the actual batteries themselves to be easily removed without tools.
• Use labels not QR codes
QR codes take too long to use on a fast-moving conveyor belt. Instead, use clear simple labels.
With lamps and batteries removed, waste luminaires are loaded onto a conveyor belt and shredded by powerful machinery. The metal, plastics, PCBs and other materials and then separated using AI-powered cameras and air jets, which blow the fragments into different hoppers.
Metals such as steel, aluminium and copper are extracted and sold on for further processing. The PCBs are ‘urban mined’ at specialist smelters in Sweden and Canada where gold, copper, silver, palladium and lead are recovered while also destroying the persistent organic pollutants (POPs) found in older circuit boards.
SWEEEP Kuusakoski are contracted and approved by Recolight to recycle end-of-life luminaires so that its members can comply with the Waste Electrical and Electronic Equipment, or WEEE, regulations.
• Don’t miss Circular Lighting Live 2023, Recolight’s flagship conference and exhibition taking place on Thursday 21 September 2023 at the Royal College of Physicians in London. Free to specifiers, Circular Lighting Live 2023 will feature leading experts, specifiers and policy makers who will share their insights into forthcoming standards and legislation, emerging technologies and new business models. For 2023, the organisers have moved to a bigger venue with more expansive exhibition floor and included a dedicated track for lighting designers. More info: www.circularlighting.live